Leistungsspektrum
- Feuerverzinken
- Pulverbeschichten
- Schlosserei
- Korrosionsschutz- &
Konstruktionsberatung - Schleuderverzinken
- Duplex-Systeme
- Glattblech-Fassaden
- All-in-One Service
wir beraten sie umfassend.
Die modernste Verzinkerei-Gruppe Europas
an drei Standorten
Computergestützte Prozesse, modernste Anlagen und technische Ausstattung sowie die langjährige Erfahrung unserer Mitarbeiter prägen die Arbeitsweise unserer Verzinkerei-Gruppe. Mit drei Standorten in Heek, Stadtlohn und Sulz am Neckar sind wir Ihr Ansprechpartner für optimalen Korrosionsschutz durch Oberflächenveredelung.
Unsere Stärken – Ihre Vorteile
- Extrem kurze Durchlaufzeiten
- Hochwertige Oberflächen
- Konstante Qualität durch modernste Verzinkungstechnik
- Anarbeitung, Weiterbearbeitung und Kommissionierung möglich
- Anwendungs- und Konstruktionsberatung
- Beratung in Fragen der weiteren Materialbearbeitung
- Großer, eigener Fuhrpark mit regelmäßigem Tourendienst
- Überdurchschnittlich hohe Termintreue
DIE VERZINKEREI IN HEEK – Modernste Verzinkungstechnik im Münsterland
Die Verzinkerei am Standort Heek steht mit ihrer Mannschaft aus etwa 150 Mitarbeitern für effiziente Abläufe, präzises und sauberes Arbeiten sowie ein hohes Maß an Zuverlässigkeit. Eigene Teams in der Verzinkerei, der Pulverbeschichtung und der Schlosserei bilden gemeinsam ein umfangreiches Leistungsportfolio ab. Unterstützt wird die Produktion von der Verwaltung, die für die Koordination, Logistik und reibungslose Abläufe sowie eine pünktliche Lieferung verantwortlich ist.
Höchste Sicherheitsstandards ermöglichen nahezu emissionsfreies Arbeiten in den Produktionshallen. Dabei stehen Nachhaltigkeit und eine klimafreundliche Produktion im Fokus unserer Unternehmen. Die Werkstücke unserer Kunden werden auf Wunsch mit dem All-in-One-Service abgeholt und mit dem hauseigenen Fuhrpark und einer festen Tourenplanung wieder ausgeliefert.
Nachhaltigkeit ist ein Teil unserer DNA
Nachhaltigkeit liegt uns am Herzen. Damit wir Ihnen den besten Service bieten und gleichzeitig die Umwelt schützen können, setzen wir auf umweltfreundliches Arbeiten im gesamten Betrieb.
Umweltfreundliche Produktion
Die hochmodernen Anlagen der Verzinkereien Heek, Stadtlohn und Sulz minimieren den Energieverbrauch und damit auch die Umweltbelastung. Aufbereitungsanlagen, geschlossene Stoffkreisläufe und modernste Filtertechnik sind Garant für optimale und effiziente Energieausnutzung und Ressourcenschonung.
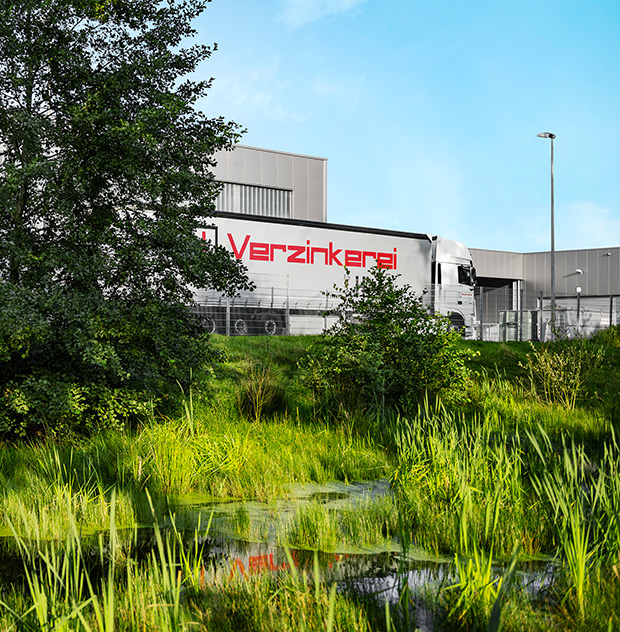
Konsequente Wärmerückgewinnung
Durch die konsequente Nutzung der heißen Ofenabgase für die Beheizung der Vorbehandlungsbäder sparen wir Erdgas. Gleichzeitig vermeiden wir im Vergleich zu herkömmlichen Verzinkungsöfen CO₂-Emissionen im Umfang von ca. 1.000 t pro Jahr. Der Energienutzungsgrad in unseren Verzinkereien liegt bei bis zu 96 Prozent.
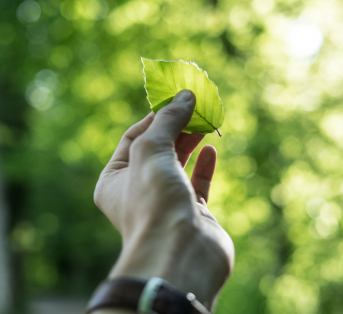